Neo Lithium Corp. informó que la Compañía ha alcanzado un hito importante con la producción de carbonato de litio en la planta piloto de su proyecto de litio Tres Quebradas («Proyecto 3Q»), situado en la provincia de Catamarca.
Utilizando la metodología alcalina mejorada, la Compañía avanzó aún más los parámetros de cristalización, así como otros ajustes menores necesarios, lo que resultó en lograr carbonato de litio de grado de batería con una pureza del 99,891%, que es aceptable por Contemporary Amperex Technology Co. Limited (CATL). por su estándar de baterías LFP. Esta metodología se aplicará al diseño de la planta piloto de carbonato de litio del proyecto en el estudio de factibilidad que está llevando a cabo Worley y se espera que esté terminado para fines del tercer trimestre de 2021.
La composición de impurezas en el carbonato de litio es la siguiente:
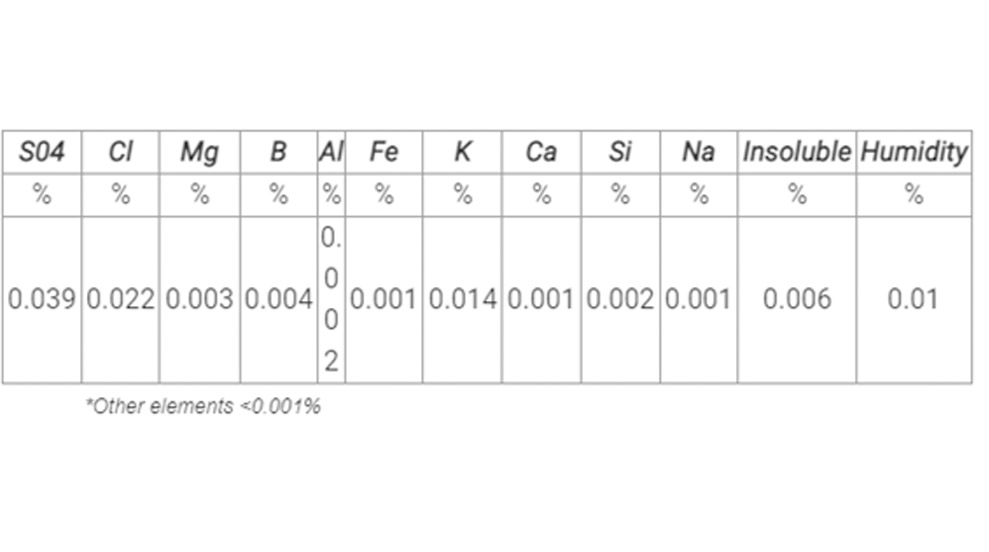
La Compañía ahora convertirá la Planta del modo por lotes al modo continuo para producir grandes muestras para la certificación de especificaciones. Neo Lithium ya ha enviado muestras a CATL en China para su propio análisis químico.
“Hemos alcanzado nuestro objetivo de producir carbonato de litio de alta calidad mientras minimizamos el consumo de reactivos y la huella de agua dulce”, afirmó Waldo Pérez, presidente y director ejecutivo de Neo Lithium. «Ahora estamos listos para completar el estudio de viabilidad con los parámetros finales alcanzados en la etapa de prueba».
El proceso de la planta piloto
Neo Lithium recibió la Planta construida por el Instituto de Investigaciones Tecnológicas de la Universidad de Concepción, Chile en febrero de 2019.Los ingenieros de la Compañía montaron la Planta en el almacén de la localidad de Fiambalá, Catamarca, ubicada a 160 km del salar donde se sitúa Tres Quebradas. La planta operó en lotes y tiene una capacidad anual diseñada de 50 toneladas de carbonato de litio por año utilizando salmuera concentrada del Proyecto Tres Quebradas con salmuera de litio de 3,2% a 3,6%.
La salmuera in-situ proviene del sector norte de alta ley del salar del Proyecto 3T, con una composición química inicial de la siguiente manera:
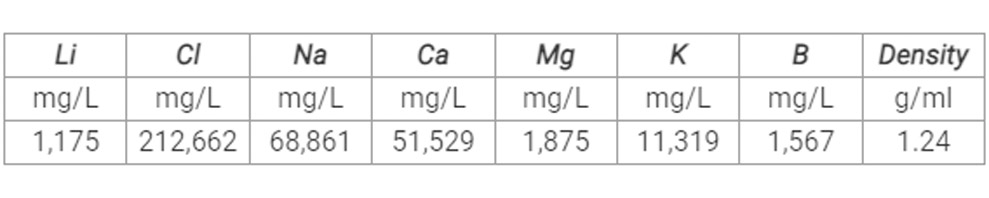
Después de aproximadamente un año, se evapora la salmuera y se eliminan el cloruro de sodio, el cloruro de potasio y el cloruro de calcio para producir salmuera concentrada con la siguiente composición:

La Planta produjo el primer lote de carbonato de litio con 99,1% de pureza en septiembre de 2019 y en marzo de 2020 los ingenieros lograron una pureza de 99,535% siguiendo el proceso descrito en el Estudio Preliminar de Factibilidad presentado en mayo de 2019. Este proceso utiliza una fase de extracción por solvente (SX-B) para la remoción de boro, una fase de sulfatación para remoción de calcio usando sulfato de sodio y una fase de encalado y carbonatación para remover magnesio y cualquier resto de calcio.
En ese momento, el equipo técnico de la Compañía diseñó un proceso más eficiente para producir carbonato de litio de mayor pureza con un menor consumo de agua dulce, reactivos y energía. Este proceso se denominó ruta alcalina y en este proceso la fase de sulfatación para la eliminación del calcio se cambia por una fase de alcalinización con hidróxido de sodio. La primera producción de carbonato de litio con este proceso alcanzó un 99,599% de pureza en marzo de 2020 y un 99,797% de pureza en enero de 2021. La empresa ha alcanzado el objetivo final del 99,891%, que se considera aceptable como producto final de material de alta calidad para baterías para la producción de baterías LFP por CATL. Este proceso se utilizará como diseño final para el estudio de viabilidad programado para ser completado por Worley a finales del tercer trimestre de 2021.
La Compañía tiene hoy alrededor de 50 toneladas de salmuera concentrada lista para ser convertida en carbonato de litio por la Planta y también ha actualizado los estanques piloto para imitar el diseño del estanque de los parámetros del estudio de factibilidad. Desde la llegada de la Planta se han producido más de 30 lotes de carbonato de litio y se han logrado los objetivos finales de calidad. La siguiente fase es configurar la planta en modo continuo para producir muestras de mayor volumen para las pruebas de especificación final y la certificación final.